İşleminiz Devam Ediyor.
Lütfen Bekleyiniz...
Lütfen Bekleyiniz...
Machining Operations Training
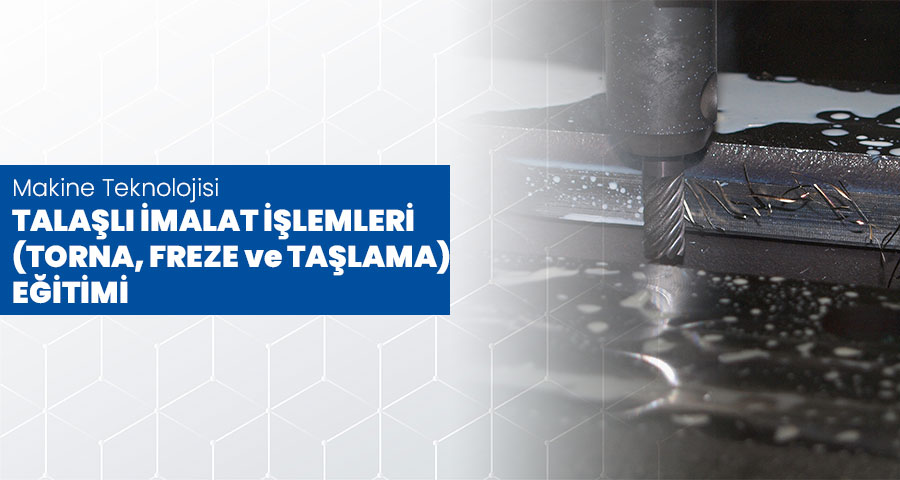
MANUFACTURING OPERATIONS 64 HOURS MACHINE TECHNOLOGIES
1. Definition 2. Types of Lathes 3. Universal Lathe Machine and its Parts A. Classification of Lathe Cutters 1. According to The Equipment a. Tool Steel Chisel b. Serial Steel Chisel c. Hard Metal Inserts 2. According to Their Form a. Right and Left Wood Chisel b. Right and Left Side Chisel c. Forehead Turning Chisel d. Channel Chisel e. Screw Chisel f. Internal and External Profile Chisel g. Hole Chisel h. Chisel Pens B. Getting to Know the Tools of Lathe Tool Tools and Selecting Tool and Choosing the Pen According to the Job C. Choosing the Way of Sharpening the Pen According to the Operation to Be Performed, D. Choosing a Stone to Sharpen the Chisel in Accordance with the Safety Rules E. Sharpening the Right and Left Wood Chisel F. Sharpening the Right and Left Side Chisel G. Deburring Sharpened Pencils with Gas and Oil Stones 2. CONNECTING THE BREAKER A. Tool Suspensions a. Straight Handle Suspensions b. Hard Mine Tip Suspensions c. Chisel Suspensions d. Suspensions Bars e. Screw Pen Suspensions f. Special Suspensions g. Chisel Suspensions, attachment of the Suspensions B. Connecting the Cutter on the Tailstock Axis C. Suitable Cutting Conditions 1. Theory of Cutting 2. Sharpness of the Cutting Edges 3. Proper Arrangement of the Cutter According to the Process 4. Finding the Angles of the Cutter from the Tables D. Cutting Fluid a. Function in cutting b. Effect on the Life of the Cutter c. The Impact on the Work Surface Quality CONNECTING WORKPIECES
1. Universal Mirror with Three and Four Legs 2. Independent Chuck 3. Perforated Flat Mirror 4. Swivel Mirror 5. Combined Mirror 6. Magnetic Mirror 7.Collets 8.Work Patterns
FACE LATHE
TAIL HOLE DRILLING 1. Choosing the Spot Drill Suitable for the Diameter, Place of Use, and Purpose of the Part to Be Turned, 2. Choosing the Center Drill Fastening Tools on the Lathe a. Mandrel b. Pliers 3. Preparing the Lathe and the Surface of the Work for centering, 4. Open the Tailstock Slot. a. Protective Countersink, b. Protective Countersink CYLINDRICAL TURNING A. Connecting Workpiece Between Chuck Tailstock B. Connecting Between Two Tailstocks 1. Connecting the Swivel Mirror 2. Connecting the Swivel to the Workpiece 3. Connecting the Workpiece Between Two Tailstocks in a Swivel Chuck 4. Checking the Runout of the Workpiece C. Cylindrical Outer Surface Turning STEPPING LATHE A. Connecting the Workpiece Between the Chuck Tailstock B. Select and Prepare the Appropriate Right and Left Side Chisel C. Stepping Surface Lathe D. Lathe Steep Side Surfaces E. Chamfering levels GROOVING A. Connecting Workpiece Between Chuck Tailstock B. Connecting the Channel Chisel C. Setting the Number of Periods for groove lathe D. Groove lathe E. Turning Groove Sides F. Trimming CONICAL TURNING Taper turning the Shield 1. Adjusting the Shield to the Appropriate Angle Tailstock with taper turning 1. Shifting Tailstock According to Taper Ratio 2. Checking Tailstock Runout Checking Taper with Sleeve, Gauge, or Micrometer KNURLING A. Knurls 1. Types of Knurls a. Flat Knurling b. Knurling tools pivot B. Preparing the Machine for Knurling 1. Arrangement of the knurls 2. Adjusting the Speed knurling 3. Setting the Proper Feed for Knurling 4. The Process of knurling B. Control of the Knurling Surface C. Oil usage Importance MANUAL OF HOBBING 1. Drilling and Countersinking of the Part in Accordance with the Screw Size 2. Selecting and Connecting the Machine Manual and Tools 3. Manual of the Lathe 4. Opening the Screw Using Oil 5. Checking the Opened Screw UNSCREWING WITH A SCREW PLATE 1. Turning the Part 0.1 – 0.2 Mm Smaller Than the Screw Diameter 2. Screw planting properly 3. Die Nut Suitable for Screw, Selecting the Threading Head and Connecting the Head to the lathe 4. Using the Appropriate Oil for unscrewing 5. Opening the Screw with a Screw plate 6. Checking the Opened Screw 13. BASIC MILLING OPERATIONS Milling Machines 1. Definition 2. Types of Milling Machines 3. Universal Milling Machine and its Parts A. Introduction of Milling Cutters According to Their Form and usage 1. Cylindrical Mills 2.Channel Mills 3.Face milling cutter 4 Angle End Mills 5. End Mills 6.T Milling 7.Module Milling Cutters 8. Form (Profile) Milling Cutters B. Milling Cutters According to the Structure of Their Teeth 1. Threaded Milling Cutters 2. Eccentric-Turned “Fixed-Section “Milling Cutters 3. Normally "Shaped" (Pointed Tooth) Milling Cutters C. Milling Cutters According to the Materials from Which They are Made 1.Tool Steel pocketknife 2. Serial Steel pocketknife 3. Hard Metal Tipped pocketknife D. Connecting Milling Cutters to the Machine 1. Connecting the pocketknife to the Spindle 2. Connecting the pocketknife to the Mandrels 3. Connection of pocketknife with Chucks and Sleeves E. Titles 1. Universal Heads 2. Additional centric Heads a. Introducing b. Usage c. Disassembly and assembly 14. CONNECTING WORKPIECES A. Connecting the clamp to the machine 1- Mouths Parallel to Body 2- Mouths Perpendicular to Body B. Connecting with clamp 1. Clamp with Screw 2. Eccentric Clamp 3. Hydraulic and Pneumatic Clamps C. Fastening with Bolts and Wedge 1. Fastening Bolts and Nuts 2. Wedge and their Types 3. Spare Parts and Their Types 4. Rules for Fastening with Bolts and Wedge D. Special connection Molds and Tools, connecting with Sine Plates E. Connecting to the Spiral head
F. Swivels Used in Milling Machines PLANE SURFACE MILLING A. Choosing a Milling Cutter Based on the Condition and Size of the Plane Surface B. Explanation of the Table Progress Direction According to the Direction of Rotation of the Milling Cutter C. Depth of Cut and Feed Appropriate Adjustment for the Job INCLINED FACE MILLING A. Milling of Vertical Surfaces 1. Connecting the Machine with Appropriate Clamping Tools for Vertical Milling 2. Checking the Correctness of Connections B. Inclined Face Milling 1. Connecting the Work to the Machine Using the Appropriate Fastening Devices and Tools to Be Able to Perform Inclined Face Milling 2. Checking the Correctness of Connections
17. SLOT AND POCKET MILLING A. Connecting the Workpiece Parallel to the Milling Machine Table to Open the Slot B. Choosing the Penknife to Use and the Correct connecting Methods 1. Slot Milling Cutter 2. End Mill Cutter C. Safety Precautions When Opening Slots D. Control of Opened Slots E. Pocket Opening with End Mill 18. BASIC GRINDING OPERATIONS A. Grinding Wheels 1. The Structure of the Emery Stone a. Corrosive Substances b. Join Elements c. Texture d. Hardness 2. Information on Stone Label B. Balancing Methods 1. Static Balancing 2. Dynamic Balancing C. Considerations for Connecting the Stone D. Grinding Wheel Sharpening Elements 1. Sharpening Disc 2. Sharpening Spinner 3. Diamond Sharpener E. Grinding Wheel Sharpening 19. OPERATING GRINDING MACHINES 1. Plane Surface Grinding Machines, a. Horizontal Spindle b. Vertical Spindle 2. Important Parts of Plane Surface Grinding Machines, 3. Choosing the Right Grinding Machine for the Job 4. Parts of the Cylindrical Grinding Machine 5. Connecting Tools a. Bench Vices b. Connecting Bolts and wedge c. Magnetic Table d. Business Patterns e. Spiral head and Striker Center 6. Grinding Machine Control Panel 20. PLANE SURFACE GRINDING 1. Plane Surface Grinding Machines a. Horizontal Grinding Machines b. Vertical Grinding Machines 2. Ways of Connecting Work to Plane Grinding Machines a. Magnetic Clamping b. Non- magnetic Clamping 3. Possible Malfunctions in Plane Grinding Machines and Their Elimination 4. Attachment of Wheels to Plane Surface Grinding Machines 5. The Sequence of Operations in Plane Surface Grinding 6. Rules to be Observed in Plane Surface Grinding 7. CNC Grinding Machines and their Characteristics a. Parts b. Principle of Operation c. Usage MEASUREMENT AND EVALUATION Completion of the given part by machining within the desired tolerances |